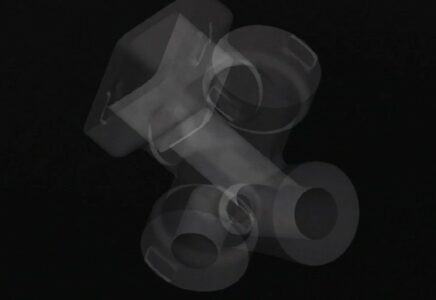
In this article we run through a typical casting design process to highlight the importance of co-operation at an early stage between designer and foundry. A typical experience based on an iterative design process might be as follows.
The role of the design engineers
The product design engineer will design casting geometry based on the component’s functional, mechanical and performance requirements. The design is then passed to the casting engineer at the foundry who also goes through an iterative process taking account of the geometry but working within the known constraints of the casting process, the requirements of the running system (which delivers molten metal to all parts of the casting) and allowing for shrinkage of the casting as it solidifies and cools. Issues identified during the design of the running system will often result in changes to the casting geometry. Further iterations of both the geometry and running system may be required during tool or mould fabrication and preparation for production. And even more changes may be needed to each element to meet production requirements or budget constraints.
The role of the production team
Clearly, this process calls for very close co-operation between the design engineer and the production team at the foundry. With a complex casting, this process can lead to additional costs and delays in production schedules, particularly when iterations are left until late in the process. This can also result in sub-optimal design as safety factors are over allowed-for in an effort to speed up design completion, resulting in higher costs, less elegant product design and greater weight.
The closer the co-operation between the customer and foundry teams and the earlier this starts in the process the easier it is to avoid constant design refinement.
Mitigating risk and keeping costs down
There are several ways of mitigating the risk to project schedules and budgets. At NovaCast, we work hard to ensure that, where possible, we fully understand the customer’s needs and are involved in the design of the casting geometry so that we can provide input from a casting process perspective at the earliest opportunity. It is important to recognise that component geometry not only affects the load carrying functionality of the casting, but also the mould construction, mould filling and material solidification processes involved in producing the casting. These processes in turn affect cycle time, casting quality, and material properties such as yield strength, ultimate strength, and fatigue resistance.
Getting the initial design as close to the optimum as possible at an early stage reduces subsequent iterations. By advising on shape optimisation and running system design while the geometry is being finalised we also help the designer to consider the implications of design decisions on material choice and usage, process interactions and overall costs.
Experience and technology combined
Much of the expertise that the foundry team add into this process was based on extensive experience and knowledge about the physical and thermal properties of various alloys and the way they interact with the moulds into which they were cast. Today, many foundries also have sophisticated computer modelling software and casting simulation systems. While these don’t replace the need for skill and craftsmanship, they can considerably speed up the design development process by identifying potential issues and optimising geometry earlier.
Conclusions
While recognising that there will always be a clear differentiation between the roles of the customer’s design engineer and the casting process engineer within the foundry, our experience has proven over the years that closer co-operation at an earlier stage delivers better outcomes for all. Innovations in computer software are speeding up the process considerably and removing many of the design iterations that have often plagued complex geometry design in the past.
At NovaCast, we encourage a close working relationship between our design engineering team and those of our customers. For help and advice or to discuss your particular requirements please contact our technical sales team on +44 (0) 1225 707466, complete our online contact form or email sales@novacast.co.uk.