Silica Sol Casting
Silica sol casting is a form of investment casting. The process is very similar except that the investment mould is made from silica sol zircon sand mixed with refractory powder. Silica sol zircon sand is exceptionally fine-grained (10-20 Microns) and can be mixed to a slurry with very low viscosity when creating the mould. The result is a casting method that delivers dimensionally accurate castings with excellent as-cast surface finishes. Crucially, the silica sol zircon moulds can withstand temperatures up to 2000°C, making them very useful when casting high temperature alloy steels and stainless steels.
Selecting the right casting process for your project
Download our review of the main casting processes and how to choose…
Why use Silica Sol Investment Casting?
Benefits of silica sol investment casting:
- Great versatility; suitable for casting most metals.
- Will allow very intricate castings to be produced with thin walls.
- Smooth surface finishes are possible with no parting line so machining and finishing are reduced or eliminated.
- Allows un-machinable parts to be cast accurately instead.
- Excellent dimensional accuracy
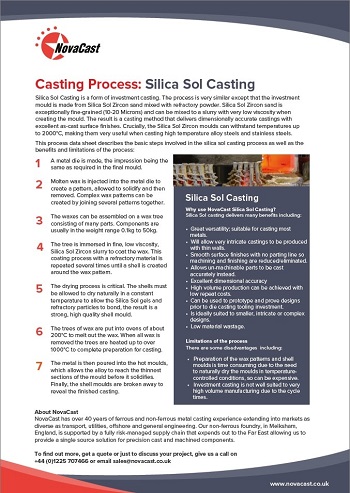
Silica Sol Process
- A metal die is made, the impression being the same as required in the final mould.
- Molten wax is injected into the metal die to create a pattern, allowed to solidify and then removed. Some complex wax patterns are fabricated by joining several separate patterns together using an adhesive.
- The waxes are then assembled on a wax tree, many parts can be put on the tree depending on size, it is common for components to be in the weight range 0.1kg up to 50kg.
- The tree is then immersed in silica sol zircon slurry to coat the wax, the slurry is exceptionally fine with low viscosity resulting in an excellent as-cast surface finish. The slurry is coated with a refractory material and the process is repeated several times until a shell is created around the wax pattern.
- The drying process is critical. The shells must be allowed to dry naturally in a constant temperature to allow the silica sol gels and refractory particles to bond, the result is a strong, high quality shell mould. The trees of wax are put into ovens of about 200 degrees to melt out the wax.
- When all wax is removed the trees are heated up to over 1000 degrees to complete preparation for casting.
- The metal is then poured into the hot moulds, which allows the alloy to reach the thinnest sections of the mould before it solidifies.
Limitations of the process:
There are some disadvantages to this process including:
- Preparation of the wax patterns and shell moulds is time consuming due to the need to naturally dry the moulds in temperature-controlled conditions, so can be expensive.
- Investment casting is not well suited to very high volume manufacturing due to the cycle times.
To discuss your requirements, call a member of NovaCast’s team on +44 (0) 1225 707466, send us a message here or email sales@novacast.co.uk.