Gravity Die Casting
NovaCast specialises in producing high quality gravity die castings at its Melksham foundry. Our non-ferrous casting foundry is ideally suited to producing medium-run components from aluminium and other non-ferrous alloys for applications across a wide range of industries including automotive, defence, marine, complex machinery manufacture, and many others.
Gravity die casting is a permanent mould casting process where molten alloy is poured into a mould with no force, other than gravity. This results in castings that far less porous than some other casting processes. The process produces dimensionally accurate, very high quality surface finishes with thin walls and cast-in inserts, so intricate shapes can be cast rapidly and little subsequent machining is required.
Top Gravity Die Casting Tips
Here are the Top 10 Tips for designing problem-free gravity die casting geometry

Why use NovaCast Gravity Die Casting?
Gravity die casting delivers many benefits including:
- Excellent dimensional accuracy
- Smooth cast surfaces
- Thinner walls can be cast allowing intricate shapes
- Inserts, such as threads, heating elements and high-strength surfaces can be cast-in
- Secondary machining is reduced or eliminated
- Production rates can be rapid making longer production runs possible
- Tensile strength is higher than with sand casting
- Specialist aluminium casting foundry
Gravity Die Casting Process
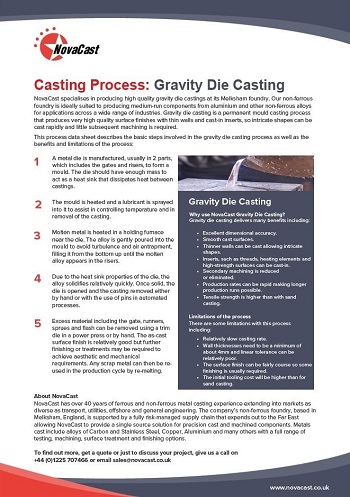
- A metal die is manufactured, usually in 2 parts, to form a mould.
- The mould is heated and a lubricant is sprayed into it to assist in controlling temperature and in removal of the casting.
- Molten metal is poured into the mould.
- Once solidified, the die is opened and the casting removed either by hand or with the use of pins in automated processes.
- Excess material including the gate, runners, sprues and flash can be removed using a trim die in a power press or by hand.
- Scrap metal is then re-used in the production cycle by re-melting.
Limitations of the process:
There are some disadvantages to this process including:
- The initial tooling cost will be higher than for sand casting
- Longer production runs help to keep unit costs down and make gravity die casting competitive with other processes
To discuss your requirements, call a member of NovaCast’s team on +44 (0) 1225 707466, send us a message here or email sales@novacast.co.uk.
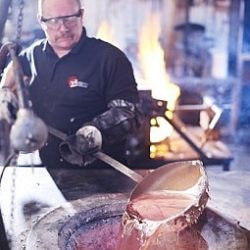
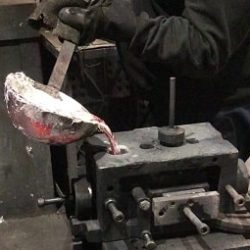
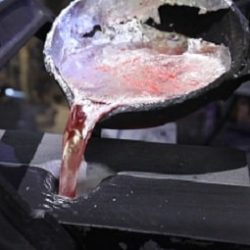
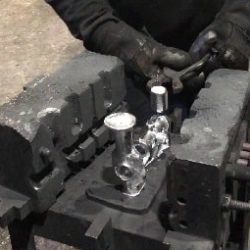
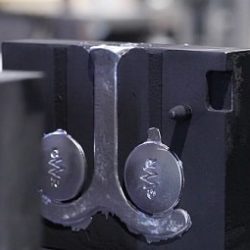
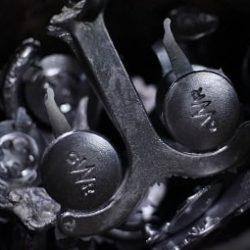
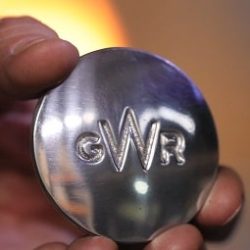
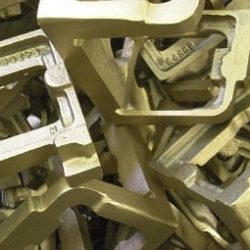
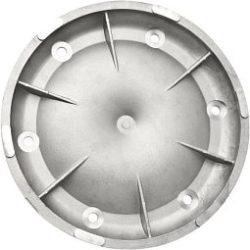
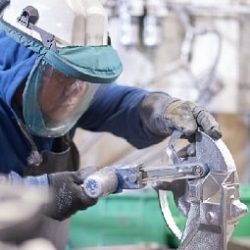