3D Printing of Casting Patterns
Prior to the introduction of 3D printing technology, foundries had limited options for master pattern production. The fabrication of patterns was often difficult and carried out by highly skilled patternmakers.
This was time-consuming and expensive. Prototyping of the cast component was usually required to ensure final dimensions were achieved and casting defects eliminated.
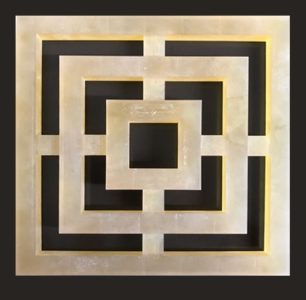
Rapid Prototyping
Find out how 3D printing is making its presence felt in the modern foundry…
NovaCast is at the forefront of the metal casting industry in employing 3D printing in the production of prototype patterns in its casting processes. The technology has emerged as a significant additive manufacturing process in recent years, particularly in rapid prototyping and short-run production of complex geometric shapes.
NovaCast uses the Selective Laser Sintering (SLS) process, which integrates seamlessly with its 3D modelling and casting simulation software to produce patterns for prototyping of cast components.
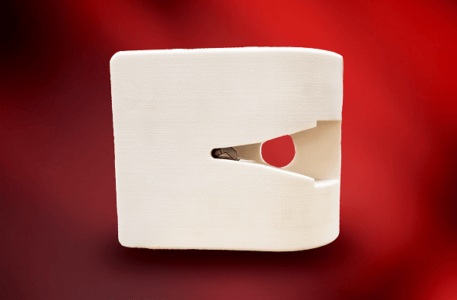
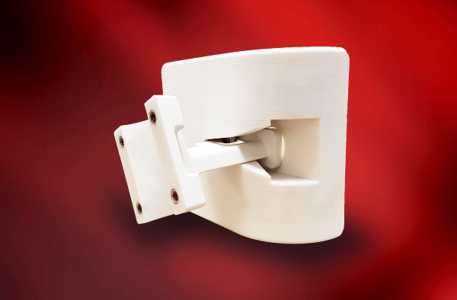
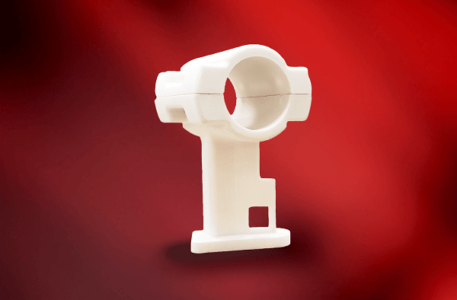
Employing the latest technology in this way allows NovaCast to deliver several important benefits to its customers including:
- Engineering design freedom: 3D printing allows casting geometries to be far more complex and accurate, with thinner walls and greater freedon to replace multi-part fabrications with single castings.
- Lower costs: 3D printing considerably reduces the time, processes and skills needed to produce a pattern. Engineers can go direct from digital files to physical pattern quickly and subsequent design modifications are also achieved rapidly.
- Waste reduction: Traditional patternmaking processes, particularly those involving the machining of metal patterns, require far more raw material than 3D printing, which is an additive manufacturing process requiring only the material used in the printing process.
- Production speed: Traditional patternmaking can take weeks for the original pattern and even more time if modifications are needed. 3D printing can take just a few hours with little supervision required once the process is under way.
- Reduced Storage: Physical patterns have traditionally been stored at the foundry for subsequent re-use. 3D printing considerably reduces the need for this as new patterns can be quickly and cheaply reproduced.
To discuss your requirements, call a member of NovaCast’s team on +44 (0) 1225 707466, send us a message here or email sales@novacast.co.uk.