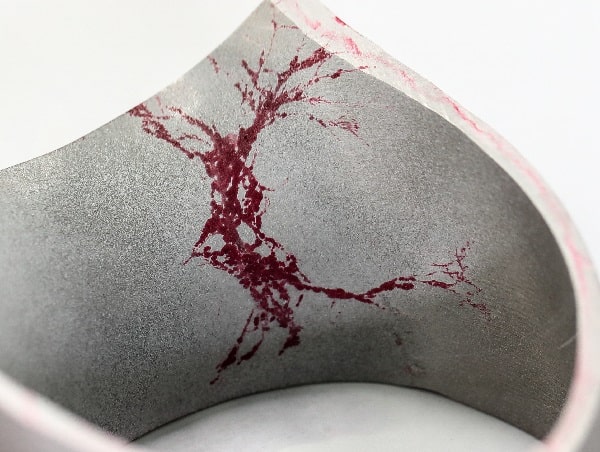
In a perfect world, every casting would be free of defects and perform exactly and reliably to design specifications. The reality, however, is that casting metal is a process subject to a multitude of factors that affect the way that an alloy reacts throughout the process. The inevitable result is that defects are an inherent part of the casting process. For some castings, the presence of defects or inconsistencies in the cast metal structure may be of limited importance as they may not affect the performance of the component. For other components, subject to extreme stress, pressure, heat, or cold, for example, the presence of casting defects may be critical.
Understanding the often-conflicting factors involved, mitigating risks, refining processes, and bringing to bear many years of foundry expertise will reduce the number and significance of defects but ultimately, the only way to be sure that a casting meets specification is to test it.
In this article, we look at the different testing options available but with particular focus on the differences between destructive and non-destructive testing of cast metal components, and the reasons why each may be deployed.
Horses for courses
Clearly, the most obvious difference between non-destructive testing and destructive testing is that the former can be performed on a component without compromising its structural integrity or diminishing its value.
Beyond this, however, the choice between the testing options really comes down to what you are trying to test for. Destructive testing is generally used to analyse the behaviour of a cast component until the point of failure. This allows us to assess the performance characteristics of the component against industry standards, or against the specific performance requirements of the component under real-life environmental stresses and usage, for example.
Non-destructive testing, by contrast, specifically avoids the destruction of the component but can be used to reveal the presence of surface and sub-surface anomalies, that may or may not fall within the design specification of the component, giving the option to accept or reject it, refine the casting process, or modify the design geometry to reduce the occurrence of the defect.
So what are we looking for?
With a destructive test, we are likely to be looking for extremes of physical properties up to the point of failure within a specific cast component. This analysis allows us to gauge feasibility in real-world usage. These tests can include the following:
- Tensile test: this involves analysis of strength properties such as the plastic deformation, reduction in diameter, and point of failure resulting from subjecting the sample to tension.
- Compression test: this involves the measurement of the component’s behaviour under a crushing load until failure. By testing the component across various axes, data can be gathered regarding yield strength, compressive strength, and point of yield.
- Bending test: This flexural test looks for ductility when parts of the component are subjected to loads causing it to bend. The combination of compressive stress on the inner edge and tensile stress on the outer edge of the bend are measured to reveal the elastic modulus, flexural strength, and strain.
- Hardness test: This test seeks to determine the resistance of the alloy to permanent deformation following the controlled application of load to the surface of the component. The size and depth of any indentation are measured and analysed using one of several testing processes including the Brinell Hardness Test among others.
- Torsion test: Subjecting the component to twisting forces often found in vibrations and operational motion allows us to gauge the resistance to deformation providing data on the shear modulus, rupture modulus, and yield strength of torsion.
With non-destructive testing, we are much more interested in revealing specific casting defects that could be on the surface, within the cast structure, or both. Examples of these would be porosity, airlocks, blowholes, non-metallic inclusions, various shrinkage defects, segregation caused by non-uniform chemical distribution in alloys, cold shuts, hot tears, and cracks.
Non-destructive tests available through NovaCast include:
- Visual Inspection. A variety of surface imperfections in a casting, such as sand holes, surface shrinkage, blowholes, etc. can be picked up by careful visual inspection, so this is usually the starting point.
- Pressure Testing is used where part of the specification is for a pressure-tight casting; air, water or inert gas are used to test the casting for leaks under pressure.
- Liquid Dye Penetrant and Fluorescent Powder can be suspended in penetrating oil and applied to the surface of the finished casting. Surface cracks and flaws are immediately visible on application of the developer or in the presence of ultraviolet light.
- Radiographic inspection (X-Ray) is extremely effective in identifying internal holes, cracks or inclusions near the surface of the casting. The cast component is exposed to radiation and the image created on the radiographic film indicates changes in casting density. In addition to identifying defects, the x-ray can be retained as a permanent record of the test results.
- Magnetic Particle Inspection is particularly useful in identifying the location of surface discontinuities in ferrous metal. It can sometimes also indicate subsurface defects if the magnetizing force is strong enough to produce a leakage field at the surface. If fine iron filings or particles are brought into contact with the component, they take a position that roughly outlines the boundaries of the leakage field. A low velocity air stream blows excess filings away, leaving the defect outlined by the remaining particles. The particles can be applied while the magnetizing current is flowing (continuous method) or after the current is off (residual method).
- Ultrasonic Testing is an expensive process due to the skill requirements of the technician needed to interpret the results. This process is used to identify internal defects by transmitting high frequency acoustic energy (sound) into a casting. The high frequency acoustic energy travels through the casting until it hits an opposite surface, interface, or defect. The interface or defect reflects portions of the energy which are collected in a receiving unit and displayed for the analyst to view. The pattern of energy deflection can indicate the location and size of an internal defect, as well as the wall thickness and nodule count of ductile iron.
- Eddy Current Inspection is used to detect minor cracks and defects near the surface and discontinuities in the casting caused by material changes. This is a fairly expensive process and is limited to electrically conductive metals.
The choice of non-destructive tests is extensive but selecting the most appropriate for any particular application will depend on the component geometry, alloy selection and performance specification of the casting. NovaCast advises its customers on the most appropriate testing methodology for each casting and works closely with them throughout the design and production stages to ensure that casting defects are minimised.
Practical considerations
As stated above, the choice between destructive and non-destructive testing can depend largely on what information you are looking for. In addition, however, there are some practical considerations that can also influence the choice of testing method.
Apart from the obvious preservation of the asset, non-destructive testing can be more cost-effective in the long run as there is less need to provide multiple sacrificial samples – a significant cost on high value components. Non-destructive testing also allows for continuous monitoring and routine inspections that provide real-time results, and it can be performed on-site or in the field without the need for transportation to a testing facility.
At NovaCast, we encourage a close working relationship between our design engineering team and those of our customers. For help and advice or to discuss your particular requirements please contact our technical sales team on +44 (0) 1225 707466, complete our online contact form or email sales@novacast.co.uk.