Sand Casting
Sand casting is one of the oldest casting techniques and retains its place in modern manufacturing due to its versatility. Sand cast components can range in weight from a few grams to several tonnes, in complexity from simple shapes to complex geometries, and be used with virtually any alloy. The production of complex, mainly non-ferrous sand cast components is one of the the core business activities of NovaCast’s UK Foundry. In it’s basic form, it is the simplest production method but has many advantages, particularly for short-run or complex castings with multiple cores or for larger castings.
NovaCast is able to produce sand moulds by hand, using greensand for smaller quantities and resin or petro bonded techniques using a semi- automated process for larger quantities. Up to 70% of sand used in the process is reclaimed and re-used so meeting our environmental objectives.
Casting Design Considerations for Design Engineers
Some factors inherent in casting processes that can affect component design…
Why use NovaCast Sand Casting?
Sand casting has several benefits including:

- Low tooling costs and fast set-up compared to investment or die casting.
- Large casting sizes possible. NovaCast is able to cast aluminium alloys up to 110kg and ferrous alloys up to 3000kg through our partner foundries, using sand casting methods.
- Complex and intricate castings can be achieved with multiple internal cores.
- It is possible to achieve low gas porosity for pressure tight castings.
- Up to 70% of the sand used in the process is reclaimed.
- Very versatile; many different kinds of metal alloy can be cast using this process.
- Sand casting is best suited to low volume or complex non-ferrous castings or large ferrous castings.
Sand Casting vs Shell Mould Casting
This article compares Sand Casting and Shell Mould Casting, which uses phenolic resin to create a sand shell mould.
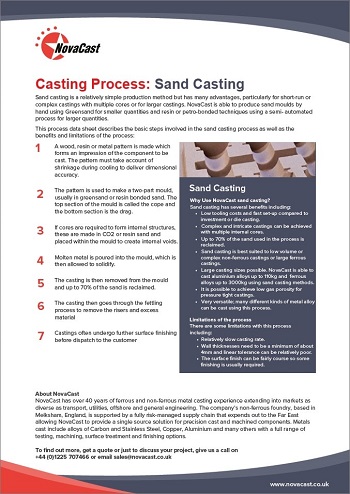
Sand Casting Process
- A wood, resin or metal pattern is made which forms an impression of the component to be cast.
- The pattern is used to make a mould, usually in greensand or resin bonded sand.
- If cores are required to form internal structures, these are made in CO2 or resin sand.
- Molten metal is poured into the mould, which is then allowed to solidify.
- The casting is thenremoved from the mould and up to 70% of the sand is reclaimed.
The casting then goes through the fettling process to remove the risers and excess material
Castings often undergo further surface finishing before dispatch to the customer
Limitations of the process
There are some limitations with this process including:
- Relatively slow casting rate
- Wall thicknesses need to be a minimum of about 4mm and linear tolerance can be relatively poor.
- The surface finish can be fairly course so some finishing is usually required.
View images of the sand casting process in our “Facilities Gallery”.
To discuss your requirements, call a member of NovaCast’s team on +44 (0) 1225 707466, send us a message here or email sales@novacast.co.uk.
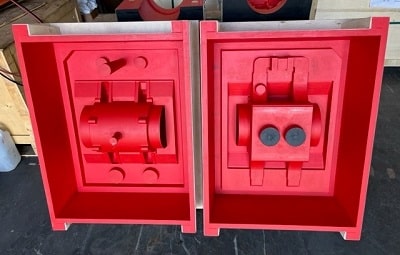
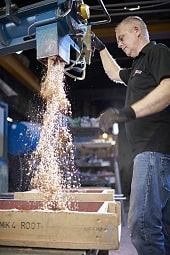
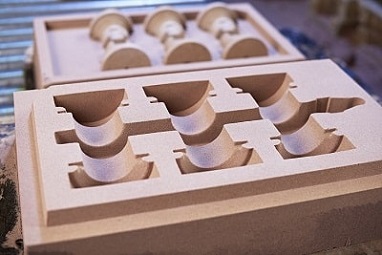
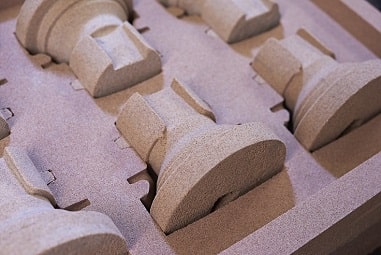
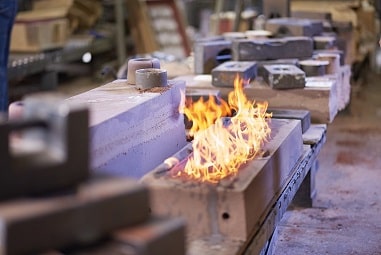
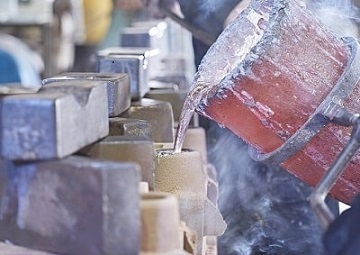
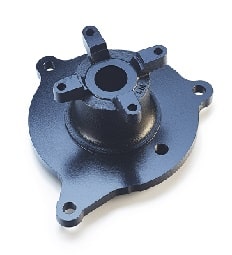
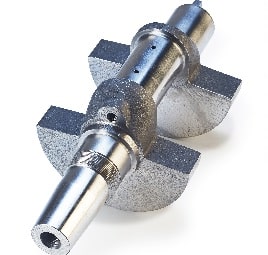
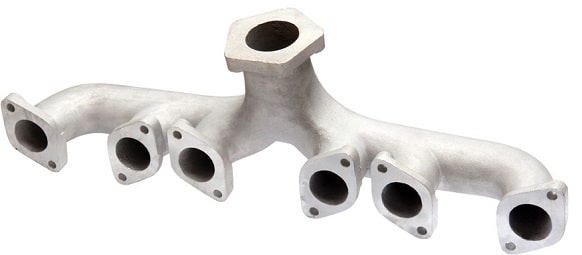
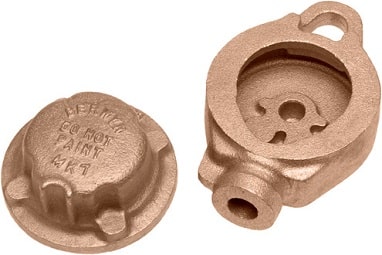
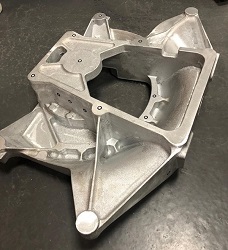
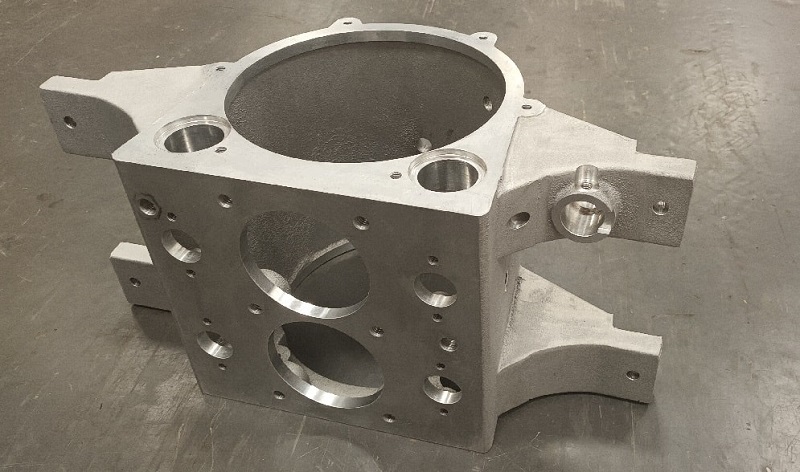

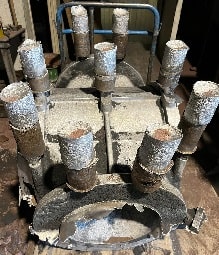
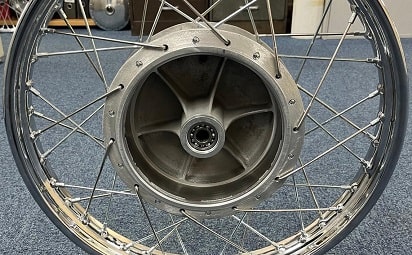