Top 10 Tips for Problem Free Gravity Die Casting
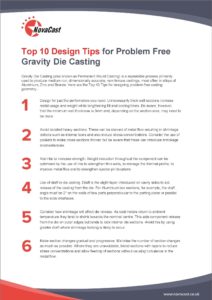
Gravity Die Casting (also known as Permanent Mould Casting) is a repeatable process primarily used to produce medium-run, dimensionally accurate, non-ferrous castings, most often in alloys of Aluminium, Zinc and Bronze. Here are the Top 10 Tips for designing problem-free casting geometry…
- Design for just the performance you need. Unnecessarily thick wall sections increase metal usage and weight while lengthening fill and cooling times. Be aware, however, that the minimum wall thickness is 3mm and, depending on the section area, may need to be more.
- Avoid isolated heavy sections. These can be starved of metal flow resulting in shrinkage defects such as internal tears and also induce stress concentrations. Consider the use of pockets to make cross sections thinner but be aware that these can introduce shrinkage inconsistencies.
- Add ribs to increase strength. Weight reduction throughout the component can be optimised by the use of ribs to strengthen thin walls, to manage the thermal profile, to improve metal flow and to strengthen ejector pin locations.
- Use of draft in die casting. Draft is the slight taper introduced on cavity sides to aid release of the casting from the die. For Aluminium box sections, for example, the draft angle must be 2° on the walls of box parts perpendicular to the parting plane or parallel to the slide interfaces.
- Consider how shrinkage will affect die release. As cast metals return to ambient temperature they tend to shrink towards the nominal centre. This aids component release from the die on outer edges but tends to lock internal die sections. Avoid this by using greater draft where shrinkage locking is likely to occur.
- Make section changes gradual and progressive. Minimise the number of section changes as much as possible. Where they are unavoidable, blendsections with tapers to reduce stress concentrations and allow feeding of sections without causing turbulence in the metal flow.
- Be aware that sharp angles can cause cooling problems. Sharp angles cause high thermal gradients as heat dissipation is hindered. Similarly, sharp re-entrant angles also cause hot spots. Differential cooling rates induced by corners can lead to shrinkage tears and distortion defects.
- Focus on junction design to avoid heavy mass concentrations. Due to the nature of the geometry of L, T, V, X and Y junction sections, each results in an area of metal with higher volume. This can cause hot-spots leading to differential solidification and localised defects or weaknesses. The flow of casting material must be carefully considered but Design Engineers can design out these potential issues by adjusting joint configuration slightly.
- Add Radii and Fillets: Fillets (rounded internal corners) and external radii (rounded external corners) are used by design engineers to strengthen corner sections and improve metal flow. Although fillets can be added without radii, best practice would be to use both in order to maintain uniform section thickness.
- Parting Line positioning. The parting line is the plane at which the two halves of the die meet. In general, the parting line should be kept as straight or flat as possible. The location of the parting line is an important decision that must take account of the component geometry and be positioned to take account of undercuts, draw, drafts, flash, flatness, dimensional stability.
To discuss your requirements, call a member of NovaCast’s team on +44 (0) 1225 707466, send us a message here or email sales@novacast.co.uk.