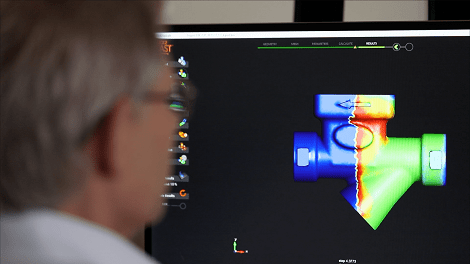
Casting Process Simulation is used by NovaCast to develop comprehensive modelling of the intended production process to determine the size and shape of sprues, runners, gates, and risers. One of the main benefits of these systems is that they make it possible for us to quickly identify areas within the casting geometry that could give rise to process related defects (micro porosity, tears, etc.).
Using these methodologies, NovaCast’s process engineers can quickly adjust the running system design to evaluate how different design options might affect defect size and location so they can be controlled or eliminated. Using computer simulation early in the design process greatly reduces the amount of guess work involved in specifying cost effective and functionally acceptable casting geometry.
Computer based casting process simulation also delivers consistency and predictability because it provides a scientific base for casting design. This makes it much easier for design engineers and process engineers within our foundry to work as a team, quickly producing the casting geometry and running system in a coordinated process.
In practice, this makes it possible to properly evaluate the overall design before tools are cut and the design is irreversibly committed to hardware. When used properly, the result is a substantial reduction in design time and tooling iterations. It is important, however, to understand that the use of casting process simulation software is not a substitute for the early input of experienced tooling and foundry engineers. It is actually a tool that helps promote closer integration of the customer and foundry teams at an earlier stage.
Much of the expertise that the foundry team add into this process is based on extensive experience and knowledge about the physical and thermal properties of various alloys and the way they interact with the moulds into which they are cast. NovaCast has sophisticated computer modelling software and casting simulation systems and while these don’t replace the need for skill and craftsmanship, they can considerably speed up the design development process by identifying potential issues and optimising geometry earlier.
If you are investigating the best option for a cast or machined component and need to call on our experience and expertise we would be delighted to hear from you. Call a member of NovaCast’s team on +44 (0) 1225 707466, send us a message here or email sales@novacast.co.uk.