In its most basic form, sand casting relies on a sand mould created in two halves, the cope and drag, with the concave shape of each mould part being formed around a pattern. The mould is filled with molten metal and cooled. Once the sacrificial sand mould is broken away the cast component is revealed. This simple but very effective casting technique has been in use for over 3,300 years and, in many ways, it has changed very little.
There are several imitations, however, as a basic sand mould cannot create intricate internal structures and requires a ‘draft angle’ or taper, needed to extract the pattern when the sand mould is made. Think, for example, of a valve body that has internal voids that simply can’t be created from a simple two-part mould. The solution is to incorporate sacrificial cores into the sand mould that form the internal structures of the casting. These cores are then broken up during the ‘shake-out’ process which removes all sand-mould elements from the component once cast.
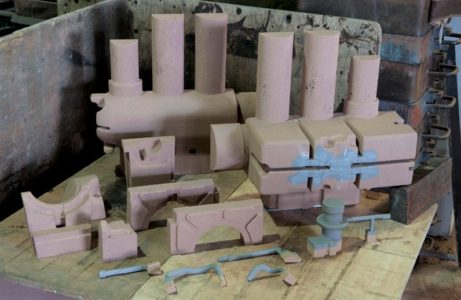
Core Properties
Creating cores is an art in itself and follows many of the principles that dictate the production of sand moulds. Most cores are made from sand with binders to add mechanical strength. It is critical that the resulting sand core meets certain criteria if it is to function effectively. As the core is manually placed into the mould it must be strong enough to handle. It must also be strong enough to withstand the forces imposed during the casting process.
At the same time, the core must be both permeable, to allow the escape of gases, and friable enough to break down easily to allow for alloy shrinkage and easy extraction from the cast component. The core material must not produce additional gases and must be resistant to break-down when exposed to high temperatures. Finally, the core surface must be as smooth as possible.
Binders are the critical ingredient
Binders transform green sand into a material that performs as needed for core making. For hundreds of years, core oil was used as the binding agent. Often, this consisted of linseed oil mixed with small amounts of resin and a thinner, such as kerosene. Today, with increasing focus on both performance and the environmental impact of the casting industry, cleaner core-making processes are used. These processes can use low temperature baking, allow easy collapse during shakeout, and produce less off gassing during the core-making process.
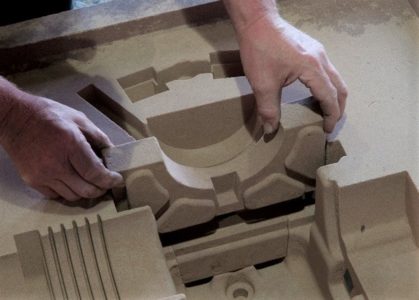
Binding Processes
Different binders are used depending on the method of core manufacture. The three main binding processes used today are: cold setting, cold-box or gas-hardened, and hot-curing.
- Cold-setting: This chemical self-setting process often uses furan resins and phenol-formaldehyde resins which are acid-catalysed. Setting starts to occur when sulphuric acid is added with reaction times being regulated by the mix of chemicals to allow for adequate working time.
- Cold-box or gas-hardening: In this process, the binder starts curing once a gas is added to the sand. The binder coated sand is packed into a core box and then sealed so that a curing gas can be introduced. The gas used depends on the binder type. Sands enriched with furan resins or epoxies can be hardened by introducing SO2 and sodium silicate, can be hardened using CO2. These gases are often toxic or odorous, so special handling systems must be used. They do have the advantage, however, that the lack of heat as the curing agent means that core boxes can be made from metal, wood or plastic.
- Hot-curing: These processes rely on heat to set the core sand. With traditional core oil binders, the core is baked in a convection oven between 200 and 250°C until the surface of the sand cures. This process forms a hard shell around the sand core, so curing is not required throughout the core. Although relatively simple, this process lacks dimensional accuracy. Another option requiring heat is the Hot-box process. This involves packing the sand-binder mix into a pre-heated core box. The method uses furan or phenolic resins and a catalyst acid-salt, which cures on contact with the hot-box or during subsequent heating. Once again, only the surface sand is usually cured, so these are often referred to as ‘shell cores’.
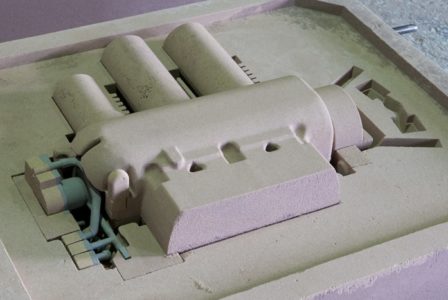
Positioning cores is usually a manual process
Once a core has finished curing it is usually finished by hand to remove any imperfections or parting lines on the surface. Multiple cores can be joined at this stage before being carefully placed into the mould by the foundry worker. Sometimes the cores need to be held in position within the mould and this can be done by using ‘chaplets’. A chaplet is a metal support that bridges the gap between the core and the mould surface to prevent the core from moving. These are often made from the same alloy as the casting because they become part of the casting and their surface must melt and fuse with the molten allow as it flows into the mould.
Cores extend the use of sand casting
Without cores, the use of sand casting would be far more limited. In addition to the ability to introduce more complex designs, internal voids and structures, cores can deliver other benefits. Even where internal voids are not needed, they may be desirable to cut down on alloy usage and component weight. So, cores allow sand casting to retain its pre-eminence in the casting market, making low-cost castings available throughout the world and in even the most technically advanced industries.
At NovaCast, we have experience in producing sand castings for use in a wide range of industries using both ferrous and non-ferrous alloys. For help and advice or to discuss your particular requirements please contact our technical sales team on +44 (0) 1225 707466, complete our online contact form or email sales@novacast.co.uk.