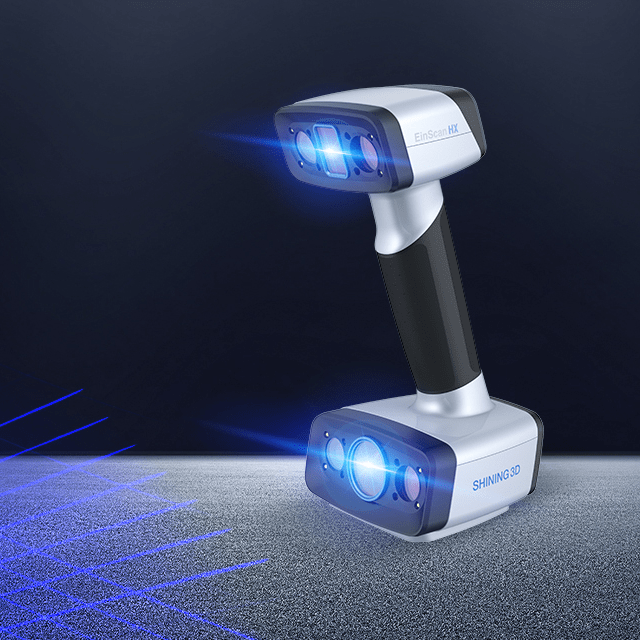
The ability to accurately reverse engineer existing castings is essential to any modern foundry. Reverse engineering could be required for a variety of reasons ranging from replication of an old casting where original patterns have been lost to improving mechanical performance or learning from an existing design to replicate or improve it. Whatever the reason, the foundry engineers must be able to accurately scan a casting and integrate the results with other digital design systems.
At NovaCast, we have just invested in Shining 3D EinScan HX supplied by 3D specialists CDG. This state-of-the-art hand-held scanning equipment and supporting software packages allow NovaCast to scan existing cast components or assemblies, import and modify the data, and then import it into existing CAD systems.
EnScan HX
The innovative EinScan HX scanner has integrated blue LED light and blue laser which opens the handheld scanner up to a wider range of object sizes. LED light scanning allows quick 3D scanning, and the blue laser is less sensitive to ambient light, making it the best choice for scanning dark or reflective surfaces. The scanner has high resolution and accuracy to meet the standards needed for most industrial applications. The EinScan HX incorporates a Rapid Scanning Mode, making it easy to print even the most complicated designs very quickly. This scanner also has a full colour camera built in to capture the detail of the scanned texture and vibrant colours of the scanned object.
Geomagic Essential and Solid Edge Software
Geomatic Essential software processes the scanned 3D data and allows it to be edited using Point Cloud and Mesh Editing. This helps in the precise alignment of the scan and allows a cross section to be produced. The data is then passed through high quality automatic CAD conversion allowing the import of all geometry into a native CAD package providing a familiar modelling environment. Further refinement of the data in Solid Edge allows NovaCast to prepare it for 3D printing.
Key Features of Solid Edge
- Reverse Engineering
- Convergent modelling
- Synchronous Modelling
- Simulation
- Generative Design
- Additive Manufacturing
The future is digital
Over recent years, some of the biggest changes in foundry production technology have come in the form of a digital transformation. At NovaCast, this has seen the introduction of CAD, casting simulation software, 3D modelling software, 3D printing, and now, 3D scanning. As Richard Phillips, MD at NovaCast commented “These days, investment in the foundry is less about casting techniques and much more about using the latest digital technology. Our Design Engineering department is now able to optimise casting geometries as never before, taking both time and materials out of the production process while reducing costs and improving component performance.”
To discuss your requirements, call a member of NovaCast’s team on +44 (0) 1225 707466, send us a message here or email mailto:sales@novacast.co.uk.
About NovaCast
NovaCast has over 40 years of ferrous and non-ferrous metal casting experience extending into markets as diverse as transport, utilities, offshore and general engineering. The company’s non-ferrous foundry, based in Melksham, England, is supported by a fully risk-managed supply chain that extends out to the Far East allowing NovaCast to provide a single source solution for precision cast and machined components. NovaCast has particular expertise in the production of pressure-tight valve and industrial pump components, complex non-ferrous castings and a wide range of precision castings for many engineering applications. Metals cast include alloys of Carbon and Stainless Steel, Copper, Aluminium, and many others with a full range of testing, machining, surface treatment and finishing options.
About CDG
Since inception, CDG have been focused on 3D Technology products and services. The key 3D Tech offered by the company is 3D Printing, 3D Scanning and 3D Software technologies. The company have formed key partnerships with the world’s leading 3D Tech manufactures including 3D Systems, Intamsys, Omni3D, Sinterit, Fusion3Design, Zmorph, Shining3D, Evatronix, Cambrio and Simcon. As such, CDG have a totally unique offering of the most advanced 3D Tech products and services.
CDG operate via four business divisions:-
- 3D Printing & Additive Manufacturing product sales;
- 3D Scanning & 3D Software product sales;
- Support Services for after sales support contracts and consumable sales;
- Replik8 On-Demand Services for 3D Printing, Additive Manufacturing, 3D Scanning & 3D Engineering.
Contact CDG in the UK on Tel. 01420 556755 or email info@cdg.uk.com