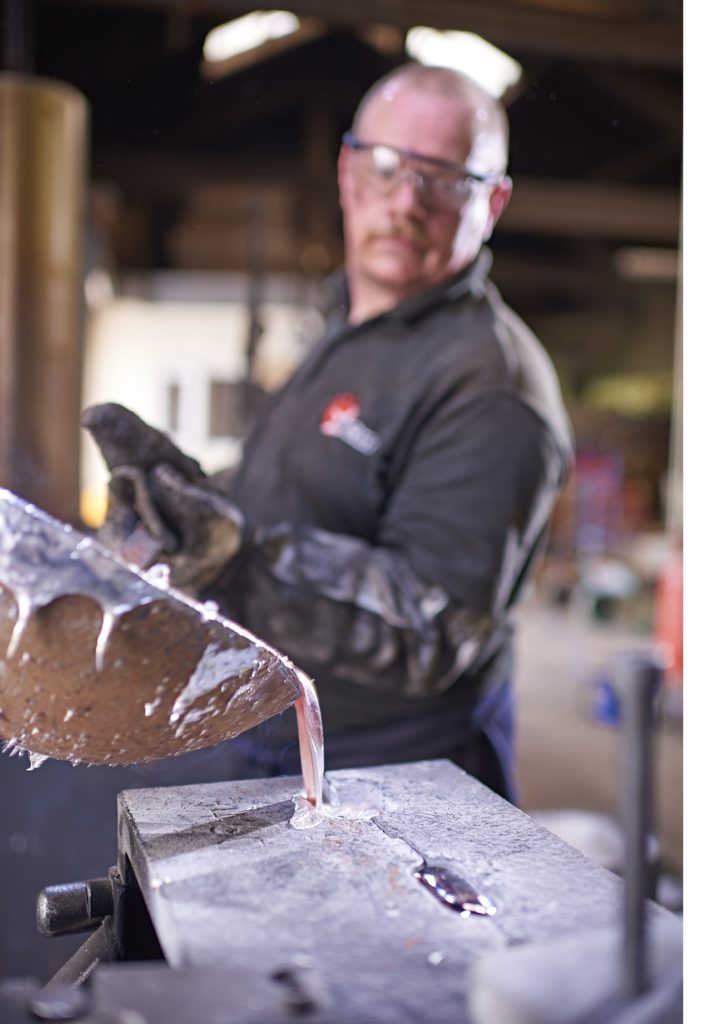
Die casting is one of the most widely used casting processes but there are significant differences between Gravity Die Casting (GDC), Low Pressure Die Casting (LPDC), and High Pressure Die Casting (HPDC). Each are casting processes offered by NovaCast, so we are well placed to explain the differences and discuss the selection criteria.
Getting metal into the mould
All forms of die casting employ a metal mould into which non-ferrous molten metal, usually an alloy of aluminium, zinc, magnesium, lead, tin or copper, is introduced. The main difference between GDC (also known as Permanent Mould Casting) and the two pressure die casting options is the way that molten metal arrives in the mould. In GDC, the molten metal is poured into the mould from above, which fills from the bottom up, purely under gravitational force. In LPDC, the molten metal is forced into the mould from below under low pressure, typically in the range 2 to 15psi. With HPDC, the alloy is injected into the mould under considerable pressure (between 1500 and 25,400 psi). In both forms of pressure die casting the pressure is maintained until the casting solidifies.
Filling speed
The high-pressure filling of the die in HPDC allows the alloy to be injected horizontally by high-speed ram very quickly (10-100ms) and, when coupled with the highly automated nature of the process, very high productivity can be achieved while the potential for human error is reduced. By contrast, LPDC is a much slower, more gentle automated process where inert gas pressure pushes alloy into the mould from below. As GDC relies on gravity to fill the mould, the process is even slower and is, therefore, less suited to long production runs. GDC can be either manual, with molten alloy poured from a hand-held ladle, or automated.
Set-up costs
The requirement to deliver molten metal under pressure into the mould in a highly automated process, makes HPDC complex and expensive to set up. There can also be a considerable difference in the tooling costs for the moulds as HPDC moulds need to be made from hardened steel and will often require internal cooling channels to dissipate heat quickly. LPDC machinery is much less complex and cheaper to set up, but the slower cycle times achievable can make the process less economic for longer runs. By contrast, GDC moulds can be made from cast iron and the lower cycling rates prevent heat build-up in the mould and allow rapid chilling of the casting. GDC also has the advantage over HPDC in that sand cores can be used to create internal voids that are not possible with the high-pressure option.
Quality, accuracy, consistency
There is a difference in the quality of casting that can be achieved from each process. The rapid filling of the mould under pressure, allows HPDC to achieve very precise and complex castings that are dimensionally accurate and with thin walls. As-cast surfaces can be very smooth, which reduces secondary machining. However, the rapid fill results in air entrapment and increases porosity, so HPDC should not be used where a guaranteed air-tight casting is required.
LPDC can also produce excellent surface finishes as well and the stability imparted by the slower fill speed reduces or eliminates tumbling, impacting, and splashing of the molten metal during the process. Hence, there is no formation of oxidation slags that can affect the purity of the castings. The result is that LPDC produces very consistent crystalline structures with greater purity and less defects, such as porosity. Formability is also good so complex geometries can be filled as the alloy is still introduced under pressure, but the process isn’t as good as HPDC for thin-walled components.
While Gravity Die Casting can’t match these attributes, the slower speed at which molten metal enters the mould does mean that less folding and turbulence occurs so less air is trapped in the casting. This gives GDC the advantage where subsequent heat treatment of the casting is required although high pressure die castings are stronger in the as-cast state.
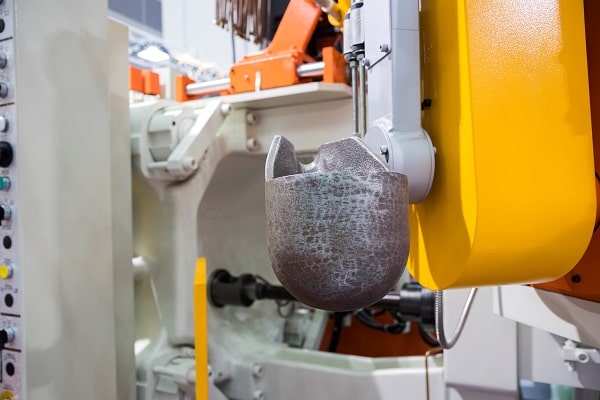
Production runs
It is clear then that both LPDC and HPDC are considerably more expensive to set up and, due to the complexity of the casting process, are less flexible than GDC. The potential for high productivity, however, means that HPDC is much better suited to stable, high-volume production runs where the unit cost of castings can be very low. LPDC can deliver excellent quality, so the selection of the process needs to weigh up the balance between cost and casting integrity.
Heat Treatment
Heat treatment of cast alloys is used to increase their strength and hardness and to change their physical, mechanical and metallurgical properties. The die casting process selected will dictate whether a cast alloy can be subsequently heat treated. A356, for example, is an aluminium alloy commonly used due to its excellent mechanical properties including high strength and ductility. It is, therefore, commonly used in low-pressure die casting and then subsequently heat treated to further enhance its properties (A356-T6). As the HPDC process introduces entrapped air and increase porosity, it cannot be heat- treated to improve mechanical properties. It is, therefore, necessary to change the allow to one that delivers the desired properties without heat treatment, such as A380 aluminium alloy.
Recent advances in LPDC
Casting processes are continually evolving so the demarcation between low- and high-pressure casting processes is not quite as clear cut as it used to be. NovaCast now offers Low Pressure Squeeze Casting as an option, which delivers the best of both processes. This is a LPDC system where very high pressure ranging from 7,250 to 43,500psi, is applied just during the solidification stage. This ‘squeeze’ stage is used to pressurize the die cavity through the runner and gates resulting in reduced porosity, better microstructure and reduced cycle times. This makes the process ideal where very high integrity, air-tight castings are required with consistently high quality combined with longer production runs.
Conclusions
The choice of casting process will often be dictated by a host of design specifications including the geometry and size of the component to be cast together with economic factors such as the production run. Sometimes GDC will be the right solution and sometimes a project will be better suited to one of the pressure die casting options. That’s why NovaCast offers a comprehensive range of casting options including Sand Casting, Investment Casting, Lost Foam Casting and Shell Mould Casting as well as the die casting options discussed.
If you are investigating the best option for a cast or machined component and need to call on our experience and expertise we would be delighted to hear from you. Call a member of NovaCast’s team on +44 (0) 1225 707466, send us a message here or email sales@novacast.co.uk.