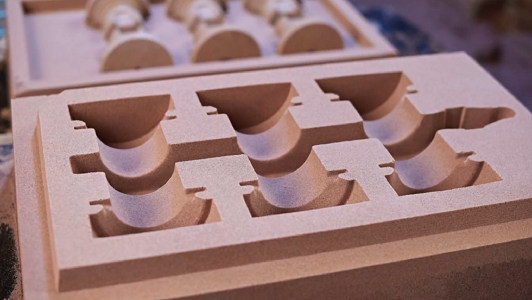
The gating system includes all those elements which connect the pouring ladle to the mould. The various elements include: Pouring Basin or cup, Sprue, Sprue Base Well, Runner, Runner Extension, In-gate and Riser.
An effective gating system should:
- Fill the mould cavity completely before the metal starts to solidify
- Control the speed that metal enters the cavity to reduce turbulence, mould erosion, metal oxidisation and gas pick-up
- Help to create the desired temperature gradient to encourage directional solidification
- Incorporate traps designed to capture non-metallic inclusions
Pouring Basin/Cup: Basin can be cut into the cope (top section of the mould) or added as an additional dry sand element. It acts as a reservoir allowing metal to feed smoothly into the Sprue. The basin should be full during pouring to prevent air being drawn into the sprue.
Sprue: This is the channel that connects the pouring basin to the rest of the running system. It is tapered to prevent the creation of low-pressure areas at the base, which would draw in air. It has a reservoir at its base which reduces the velocity of the molten metal as it reaches the bottom of the Sprue. This is important in reducing turbulence and erosion of the mould.
Runner: Runners are the channels that connect the Sprue to the cavity in-gates are usually located at the parting line with half the runner in the cope and the rest in the drag (lower section of the mould). During the filling process, the amount of molten metal coming from the Sprue Base should be more that that entering the in-gates to ensure that the runners remain fully filled. If the In-Gate is set lower than the runner this allows slag to be collected within the runner, preventing it entering the mould cavity. The runners should be kept as short as possible and avoid sharp corners or edges to reduce turbulence, gas entrapment and mould erosion. A short blind runner extension is often added as this acts as a trap for slag in the molten metal.
In-Gates: The in-gates are the point between the runner and mould cavity and can be positioned vertically, horizontally or at the bottom of the cavity. The objective should be to minimise erosion of the sand mould by the metal stream. This can be done by aligning the gates in the direction of the natural flow paths. Multiple gating is often used as the improved distribution means that lower pouring temperatures can be used which improves the metallurgical structure while reducing temperature gradients within the casting.
Risers: Essentially, the riser acts as a reservoir from which molten metal can be drawn into the mould cavity as solidification contraction occurs. The positioning of the risers is important in ensuring that every part of the casting is adequately served during this process and that solidification takes place from the extremities of the mould back towards the riser. The size of the risers will be calculated from the known volumetric shrinkage for the type of metal being cast.
To discuss your requirements, call a member of NovaCast’s team on +44 (0) 1225 707466, send us a message here or email sales@novacast.co.uk.