Sand casting is a traditional process dating back many thousands of years, but components produced using this process are still an essential part of our lives today. In this article we outline the sand casting process as carried out in a modern sand casting foundry, where technology and tradition are combined.
Although it dates back for thousands of years, the basic sand casting process has changed very little over that time. It remains the casting method of choice for many of the metal components that we live with every day. NovaCast’s, sand casting foundry has been established in Melksham, Wiltshire for over 36 years. You can find out more about our casting capabilities and the quality control procedures that are so important in maintaining consistency and keeping to specifications on our website. In this article, we provide a more detailed explanation of the processes involved in producing high quality sand castings.
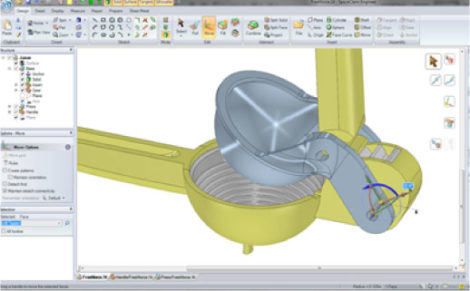
The Process begins with the customer’s enquiry and a set of specifications. These would normally include drawings of the item, produced by a draughtsman or in some cases an artist, sculptor or designer. More often than not we would be provided with CAD system files or we would create these in house for our customer using our 3D modelling software. Working with our customer, NovaCast personnel would discuss any design, tolerance, accuracy or material issues arising from these drawings and arrive at a solution.
The quality requirement and regularity of call off will influence the production process, the type of pattern equipment needed and the number of core boxes required to produce the castings to the specifications required as economically as possible. Casting simulation software is used to identify and resolve potential issues in complex castings.
Craftsmanship and experience are central to successful sand casting, particularly when it comes to making the cores that form the internal structures of the component to be cast. If the cores are complex or tolerances are critical then they will be hand-made by a craftsman coremaker using the CO2 process. Other core types will be blown on a machine using a low gas evolution self-setting process.
The moulding process would incorporate the use of a loose pattern or a set of patterns for batch production on either the self-setting Ester set process or greensand process.
The core boxes and patterns can be produced from wood, metal or resin, or a combination of all three. The choice of tooling would be governed by cost and durability over the required production period. Customers’ existing patterns can almost always be used in our process but occasionally may require modification. During the moulding process for Air Set Moulds a continuous mixer is used. The operator, at a touch of a button, can vary the ratio and reactivity of the resin and hardener that is mixed with the sand to slow or accelerate the setting time according to the size and complexity of the mould being made. The coremaker also has the option to use all new sand, a blend of new and reclaimed sand or entirely reclaimed sand.
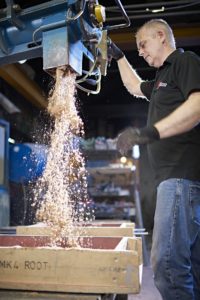
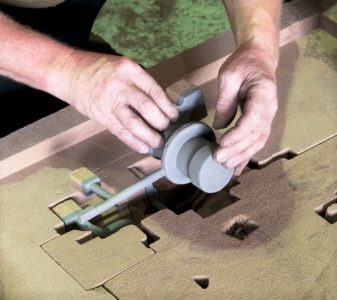
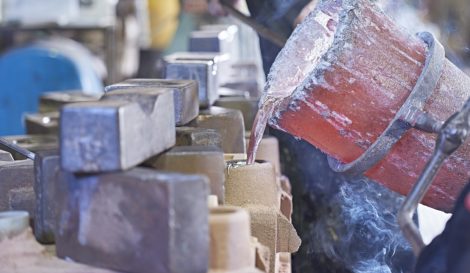
The pattern can, therefore, be faced with new washed and graded sand and backed with blended or reclaimed sand thus enhancing the surface finish of the casting. NovaCast is able to reclaim 70% of the sand used which enables us to meet our environmental targets. From new tooling and pattern equipment NovaCast will produce sample castings, so that all aspects can be checked before a production run. This enables dimensional checks as well as evaluation of the running and feeding system to ensure the integrity of the casting and greatly reduce defects, which may arise during the solidification and cooling of the castings. This is also an opportunity for the customer to decide if drawing alterations and subsequent pattern or core alterations are needed for their own purposes and the final use of the casting.
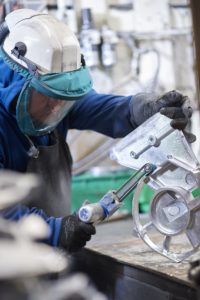
Skilled craftsmen are used in the manufacturing process and once the mould and cores have been assembled and are ready for casting, the metal is melted, treated and prepared for pouring. This can be done with the use of several melting furnaces. These fall into two groups, fixed crucible tilting furnaces which are used for large quantities of molten metal or lift out crucible furnaces used for flexibility. This flexibility enables independent melts of a variety of different metals in the same shift, which makes the operation far more efficient and keeps costs to our customers down. Temperature, modification of the metal structure and removal of gas taken into the solution during melting is carefully controlled in the furnace.
Once the castings and moulds have cooled they are taken to the sand reclamation plant, where they are broken up and all outside and internal sand is removed from the casting.
The castings then go to the fettling shop where all the running and feeding system is cut off and those areas ground or linished to the correct profile. All surfaces will then be either sandblasted or shot blasted to ensure all residue of sand is removed.
Although the casting process is very traditional, many of the castings produced today are used in specialist applications. These castings may need further surface or heat treatments to enhance performance. These processes are carried out at this stage along with a variety of inspections, tests and quality control procedures.
If further machining is to be carried out, then inspection takes place once again after this process and finally, if surface finishing is required, such as Alocrom, Plating, Lacquering, Anodising or Painting, then final inspection takes place after this but prior to packing and dispatch to the customer. When certification is required, this can take the form of a “Certificate of Conformity” and/or “Certificate of Analysis”. Test results from test bars and coins for specific mechanical or physical properties will be recorded and certified when requested.
To discuss your requirements, call a member of NovaCast’s team on +44 (0) 1225 707466, send us a message here or email sales@novacast.co.uk.