The investment casting process is named after the process of ‘investing’ or surrounding the pattern with refractory material. The pattern itself is made of wax, so the process is also known as ‘lost wax casting’. The investment casting process has been used for many thousands of years to produce idols, ornaments, and Jewellery. It became an increasingly popular casting process throughout the 20th century, but it was WW2 that led to it becoming a more mainstream industrial process. At this time, the demand for precision, net shape manufacturing using specialised alloys that could not be shaped using traditional techniques or without extensive machining, increased dramatically.
Investment casting has since spread to many commercial and industrial applications where complexity, precision and excellent as-cast surface finishes are required. This can be an extremely efficient process as less machining is required, which saves labour costs, and less alloy is wasted in this process compared to other casting options as less material is used in the sprues and runners. It is also an extremely versatile process, able to cast most ferrous and non-ferrous metals and alloys, including Aluminium, Bronze, Magnesium, Carbon Steel and Stainless Steel.
Investment Casting: Step-by-step
All metal casting processes involve the creation of a mould into which molten metal is poured. The outstanding precision and excellent as-cast surface finishes achieved with investment casting are the result of a very precise series of steps as follows:
- Create a metal die
Step one is to produce a precise metal die, much as you would in the die casting process. This die is not, however, used to cast metal. Instead, it is used to create wax patterns in the shape of the finished component. Creating the die is a complex process as the die-maker must take account of expected shrinkage of the wax pattern and of subsequent ceramic investment material.
- Create a wax pattern
A sacrificial wax pattern is required for each cast component. These are created by injecting hot wax into the die. If internal structures are required, then cores are placed within the die to create voids. The resulting wax pattern is a precise replica of the required casting. The quality of the as-cast surface is ensured by the precision of the die and the ability of the hot wax to enter even the finest detail.
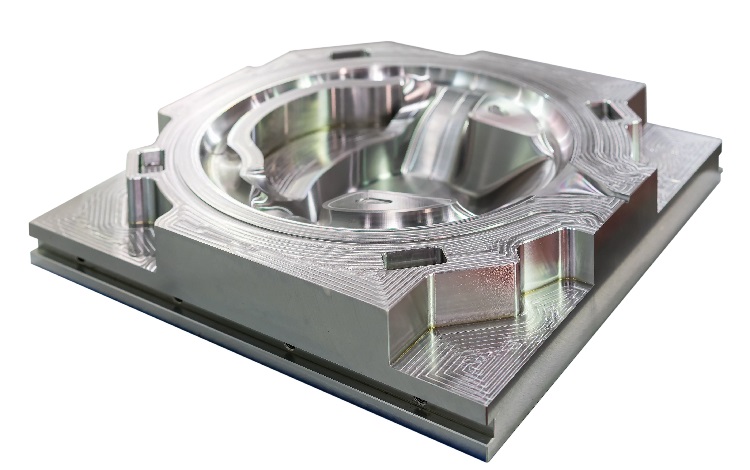
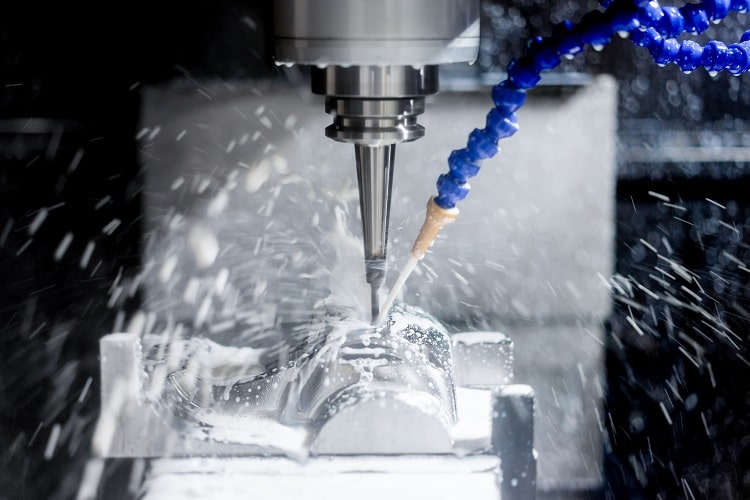
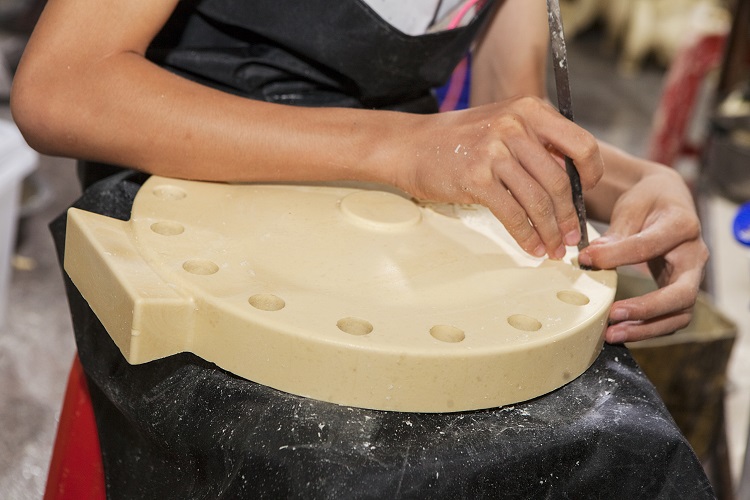
- Create a mould
The mould will ultimately be used to cast the component so it must include the gating system, which allows molten metal to travel into the mould. This includes the sprue, runners, and risers, which are attached to the wax pattern. If the component to be cast is quite small, multiple wax patterns can be joined together to form a ‘pattern tree’. This is then dipped into a refractory slurry multiple times to build up a ceramic shell around the wax elements. The thickness of the shell depends on various factors including the weight of the cast component, and the temperature of the molten alloy. Once the ceramic shell has hardened, it is inverted and heated until all the wax elements have melted and drained out leaving a hollow ceramic mould.
- Pour the molten alloy
Prior to pouring, the ceramic mould tree is heated to further strengthen the mould, burn off any remaining wax or impurities, and eliminate any water within the ceramic material. While it is still hot, molten metal is poured into the gating system and flows into each mould, aided by the high temperature of the mould. The heat retained within the mould helps ensure molten metal reaches the thinnest sections and finest detail while also allowing more uniform cooling and shrinkage of the mould and casting together, which improves dimensional accuracy.
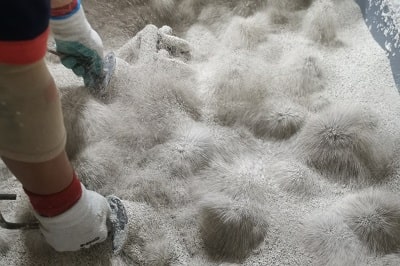
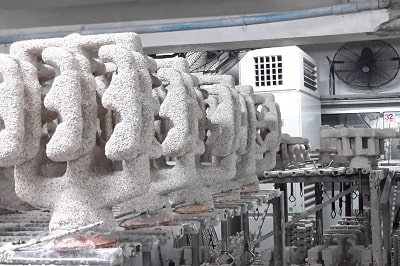
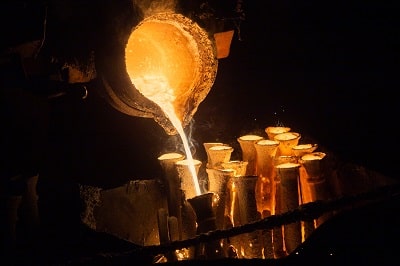
- Cooling and mould removal
Once the casting has cooled sufficiently, the ceramic mould can be removed. This is either done manually or using water jets. Each of the cast components is them removed from the ‘tree’ and separated from the gating system.
- Finishing
The final stage of the investment casting process is finishing to remove any trace of the gating system and improve the surface finish, if required. This is often done by grinding or sandblasting. Further processes, such as heat treatment of the component may follow at this stage.
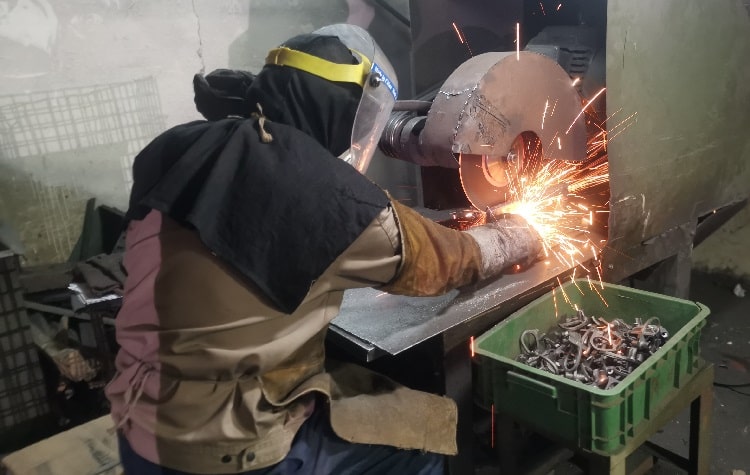
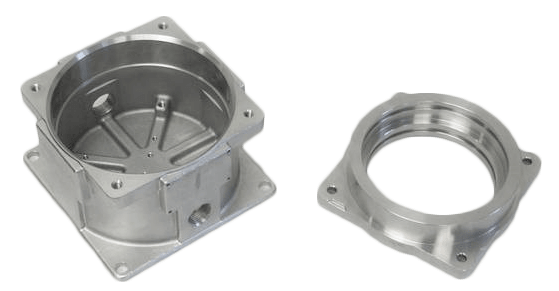
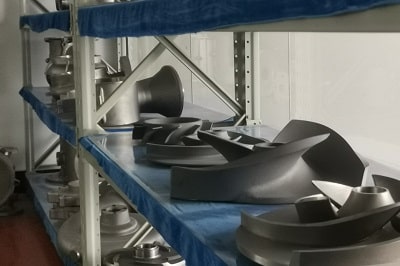
When is it appropriate to use investment casting?
As with all casting processes, there is a balance to be struck between various parameters. Cost, finish, dimensional accuracy, timescales, production volume, alloy to be cast, etc. can all influence the decision as to which casting process is chosen.
Cost is influenced by the initial set-up, which can be high for investment casting, but labour and material savings can outweigh the initial costs for longer runs. For smaller, precision-cast components, the ability to create multiple moulds and castings together, can significantly reduce production costs. Component design can be improved with investment casting as no taper (or draft) is required to extract the casting from its mould, as is the case with die casting. This also allows 90° angles to be incorporated into the design with no shrinkage or further machining required.
The ability to cast dimensionally accurate parts with as-cast surfaces that can eliminate the need for further machining is a significant benefit over other casting processes and is often the deciding factor.
How to choose your casting process
The choice is not always straight-forward as, very often, multiple casting options are available for the same component. At NovaCast, we have the capability to employ a wide variety of casting processes from sand casting, gravity die and pressure die casting to investment, lost foam, and shell casting, and can advise on the most appropriate for each project. We can also offer both ferrous and non-ferrous solutions.
Ultimately, the design specification will often include parameters which dictate the casting process that will be most appropriate but early collaboration between NovaCast’s design engineers and those of the customer can keep more options available and result in the optimal solution.
For help and advice or to discuss your requirements, call a member of NovaCast’s team on +44 (0) 1225 707466, send us a message here or email sales@novacast.co.uk.