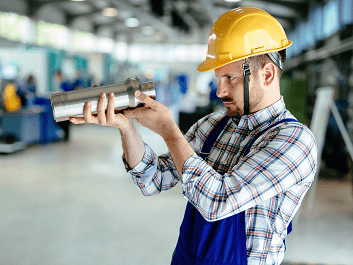
The production of high-quality castings has always been a mix of sound design, technical knowledge and the foundryman’s experience in handling and managing each stage in the casting process. More recent innovations, such as casting simulation software and 3D modelling, have helped to reduce casting defects by improving both product and gating system design. Dealing with molten metal, however, is like handling a living thing and the foundry can never be absolutely certain that any particular casting is defect-free. Where the integrity of the casting is of critical importance, NovaCast can perform a wide variety of non-destructive tests to ensure that each casting is within specification.
The following are the main non-destructive tests that NovaCast offers to its customers:
- Visual Inspection. A variety of surface imperfections in a casting, such as sand holes, surface shrinkage, blowholes, etc. can be picked up by careful visual inspection, so this is usually the starting point.
- Pressure Testing is used where part of the specification is for a pressure-tight casting; air, water or inert gas are used to test the casting for leaks under pressure.
- Dye Penetrant and Fluorescent Powder can be suspended in penetrating oil and applied to the surface of the finished casting. Surface cracks and flaws are immediately visible on application of the developer or in the presence of ultraviolet light.
- Radiographic inspection (X-Ray) is extremely effective in identifying internal holes, cracks or inclusions. The cast component is exposed to radiation and the image created on the radiographic film indicates changes in casting density. In addition to identifying defects, the x-ray can be retained as a permanent record of the test results.
- Liquid Dye Penetrant Inspection is used to find tiny cracks, pores or other surface imperfections in both ferrous and non-ferrous castings that are hard to see with the naked eye. A coloured dye in an oil solution is applied to the surface of the casting. The dye finds its way into any surface defects. A special developer is then applied and the defects become clearly visible.
- Magnetic Particle Inspection is particularly useful in identifying the location of surface discontinuities in ferrous metal. It can sometimes also indicate subsurface defects if the magnetizing force is strong enough to produce a leakage field at the surface. If fine iron filings or particles are brought into contact with the component, they take a position that roughly outlines the boundaries of the leakage field. A low velocity air stream blows excess filings away, leaving the defect outlined by the remaining particles. The particles can be applied while the magnetizing current is flowing (continuous method) or after the current is off (residual method).
- Ultrasonic Testing is an expensive process due to the skill requirements of the technician needed to interpret the results. This process is used to identify internal defects by transmitting high frequency acoustic energy (sound) into a casting. The high frequency acoustic energy travels through the casting until it hits an opposite surface, interface, or defect. The interface or defect reflects portions of the energy which are collected in a receiving unit and displayed for the analyst to view. The pattern of energy deflection can indicate the location and size of an internal defect, as well as the wall thickness and nodule count of ductile iron.
- Eddy Current Inspection is used to detect minor cracks and defects near the surface and discontinuities in the casting caused by material changes. This is a fairly expensive process and is limited to electrically conductive metals.
The choice of non-destructive tests is extensive but selecting the most appropriate for any particular application will depend on the component geometry, alloy selection and performance specification of the casting. NovaCast advises its customers on the most appropriate testing methodology for each casting and works closely with them throughout the design and production stages to ensure that casting defects are minimised.
If you are investigating the best option for a cast or machined component and need to call on our experience and expertise we would be delighted to hear from you. Call a member of NovaCast’s team on +44 (0) 1225 707466, send us a message here or email sales@novacast.co.uk.