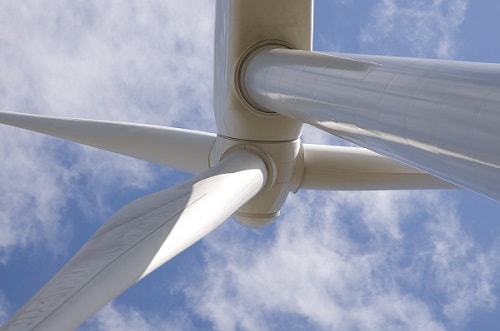
Over the years the metal casting industry has acquired a reputation as one of the worst in terms of environmental impact, largely due to traditional production practices with high energy usage going in and highly toxic emissions coming out. Add to this the massive energy demands for the extraction and production of raw metals, such as Aluminium, Iron and Copper, and it could be argued that the reputation has been fully justified.
In more recent times, however, many changes in legislation, working practices, technology and environmental awareness have led to dramatic improvements in environmental performance throughout the metal casting industry. Led by foundries like NovaCast, these changes have made the industry into one that can provide positive solutions to environmental challenges both by putting its own house in order, and by enabling more sustainable solutions throughout manufacturing industries.
This most traditional of industries found that the working practices that had served it well for decades were increasingly proven to be unacceptable in a world where resources are coming under pressure and awareness has grown about the need to live more sustainable lives. Everywhere one looked there were, and are, concerns that go to the heart of the way we live our lives. Climate change, pollution, the usage of scarce resources, water shortages and the provision of clean water supplies to name but a few.
So how has the industry changed and improved?
Looking first at the upstream elements in the process, the requirement for energy hungry raw materials hasn’t gone away but the expanding use of recycled metal that can be melted down to replace virgin supplies is playing a greater role and this is set to continue as more and more metal is recovered and recycled. Energy consumption in this area is still relatively high but the progressive switch to sustainable electrical energy from renewable sources, the greater efficiency of induction furnaces and digital management of energy consumption will play a larger part in future.
Some of the most dramatic improvements in environmental performance have occurred inside UK foundries, such as NovaCast’s Melksham facility, where improvements in materials, recycling, technology, and processes have led to greater efficiency, lower material usage and enhanced cast-component performance.
Traditionally, fluxes have been a necessary evil; vital in the foundry operation but a source of pollution that needed to be addressed. Flux manufacturers are continually trying to maintain or improve performance while reducing harmful emissions, particularly of fluorides and sulphur oxide. New granular forms of flux are reducing emissions by up to 85% without significant loss of performance as they allow less flux to be used and allow it to work in a different way. It has been found that the morphology of the flux is a significant contributor to the type and quantity of emissions.
Digital transformation
For a highly traditional industry, it is perhaps surprising that the introduction of digital technology has been one of the main drivers of environmental benefits. Using the latest CAD design solutions coupled with casting simulation software, foundries like NovaCast can design casting geometries that take weight out of components where it isn’t needed. This reduces the amount of metal needed to cast the component while maintaining its strength. Very often, this also improves the performance of the component – in many instances leading to greater efficiency and lower energy consumption in the manufactured product.
Digital design and casting simulation also allow NovaCast to test mould geometry to ensure that casting issues, such as differential solidification, localised defects or weaknesses are picked up before time and resources are spent on prototypes and tooling.
Modern digital technology also helps NovaCast’s design engineers to demonstrate to their customers how casting a single, complex part rather than assembling it from machined components or fabricating it can lead to performance improvements and lower costs. This is important from an environmental perspective because this process can also reduce material wastage and shorten the manufacturing process, using fewer resources and less energy.
3D printing is also having a significant impact in foundries and NovaCast was at the forefront of the industry in employing 3D printing in the production of prototype patterns in its non-ferrous sand casting process. Additive manufacturing processes employed in foundries have expanded rapidly in recent years, particularly in rapid prototyping and short-run production of complex geometric shapes. The result has been a reduction in resources, time and energy expended in producing moulds, patterns and tooling.
Conclusion
While it can’t be claimed that the metal casting industry has a low environmental impact, it can’t be denied that the industry has responded well to the challenges posed by the need for a more sustainable world. In essence, the casting of metal components for use in manufactured products is an environmentally sustainable process. These components can be continually recycled and cast components can enhance the environmental credentials of manufactured products used in all walks of life.
Richard Phillips, Sales Director at NovaCast is in full agreement with this point, “At NovaCast, we produce the infrastructure that enables the Irish Bike Share Scheme to operate, we produce parts for wind turbines and light-weight Aluminium components for electric vehicles. With the increasing production and use of energy from renewable sources, ever tighter legislative control and an ever increasing appetite for a more sustainable future, I have no doubt that we, and the industry in general, will continue to progress and reduce our environmental impact even further.”