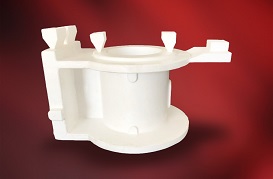
In many respects, the process involved in these two investment casting methods is similar. In both cases, a sacrificial pattern is made. In lost wax casting, this is made from a tooled mould and in lost foam casting, it may be made from a mould or carved from a solid block of foam material. A refractory material is then applied to the pattern and left to dry. The pattern material is then removed and the resulting “shell” mould is ultimately used to form the shape of the final casting. Finally, the outer shell mould is broken away to reveal the finished casting.
There are differences in the two casting methods, however, and these can ultimately determine which process is the most appropriate for a particular application. In Lost Wax Casting, the sacrificial pattern is made from wax. Once the outer shell has been created, the internal wax pattern is melted away leaving just the shell mould into which molten alloy is poured to create the casting.
In Lost Foam Casting, the sacrificial pattern is created within a closed mould using Expanded Polystyrene (EPS), machined from a block of EPS or assembled from EPS elements to form a single pattern. If risers are required for the casting, then these are made as part of the EPS pattern. When the outer shell has been created using refractory slurry and dried, the mould is ready for casting. The internal EPS pattern is left in place and sand is compacted around the mould to provide support. When molten alloy is poured into the mould, the EPS pattern instantly vaporises and the alloy fills the void to create the finished casting.
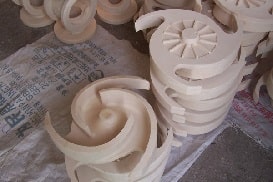
Both of these forms of investment casting can deliver complex castings with excellent ‘as-cast’ surface finishes that are dimensionally accurate. In addition, both options eliminate the need for ‘draft’, will not produce parting lines or flash around the casting, and virtually eliminate the need for further finishing processes. Of the two, however, lost foam casting can, within the right circumstances, be a less expensive option. The process is simpler with fewer manufacturing steps, EPS is less expensive than wax and it is easier to work with.
The production of complex castings can be made much easier if separate elements can simply be glued together to form a finished pattern, as is the case with lost foam casting. This means that the size and weight of the finished casting is less restricted than with lost wax casting. It is also easier to prototype using lost foam casting as the pattern can be easily made and modified by machining without having to invest in an expensive mould. Care must be taken when handling the EPS pattern, however, as they are delicate and easily damaged.
As with all casting processes, the ultimate decision regarding the most appropriate option should be made at an early stage between the engineering design team and the foundry to ensure that all parameters and requirements are considered.
For more information or to discuss your particular requirements please contact our technical sales team on +44 (0) 1225 707466, send us a message or email sales@novacast.co.uk.